PEEKの切削から射出成形への
切り替えのご提案
本ページでは、切削部品を射出成形に置換する5つのメリットと5つの懸念点(デメリット)をご紹介しています。
もしお悩みの方がいらっしゃいましたら、まずは下記フォームよりお気軽にお問い合わせください。
切削部品を射出成形に置換する5つのメリット
切削部品を射出成形に切り替えをするメリットをご紹介します。
メリット
01
コストダウンが可能
射出成形用の金型費が必要となるものの、量産の数量次第で償却が進み、償却後の製品単価は数分の1になり得ます。
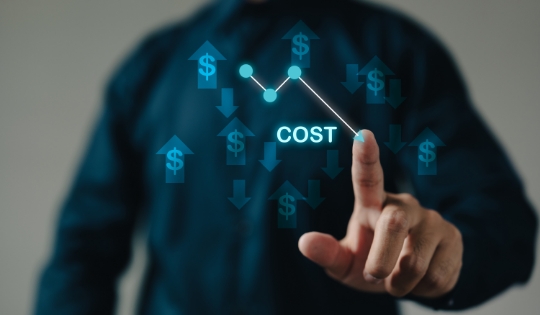
メリット
02
製品(部品)の軽量化
射出成形品は厚肉(偏肉)を嫌うため、製品(部品)の肉厚を均一にする必要があります。そのため通常、設計段階で肉盗みを設け、射出成形に適した形状にします。結果的に単体重量が軽量化されます。
ダイプラではその設計を支援させていただき、3Dでモデリングを行ない、3次元造形機でサンプルを作製し、お客様の承認後、金型製作に取り掛かりますので、相互理解のもと量産に取り掛かることができます。
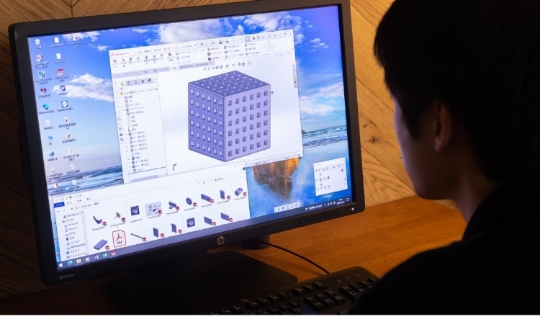
メリット
03
納期短縮(短納期対応)
切削では数十分かかる形状でも射出成形であれば、数十秒ででき上がります。1ロットの生産数が数十個、あるいは数百個ともなれば、納期にかなりの差が出てまいります。
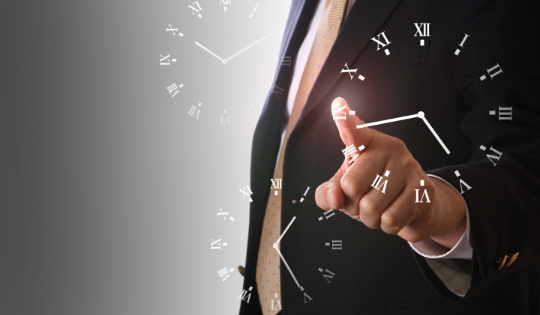
メリット
04
金属部品(真鍮、ステンレスのナットやボルト等)との一体成形ができる
切削加工で金具入りの樹脂部品を作る場合、樹脂と金具を接着材で接合、あるいは熱圧入加工で対応しますが、前者はPOMなどの難接着材では強度は望めませんし、後者は回転や引き抜き方向で十分な接合強度を得られない場合があります。
射出成形では金型に予め金属部品をセットしておき、その上から溶融した材料を流し込むインサート成形法を用いることで強固な金属と樹脂の一体部品を得ることができます。
もちろん下穴だけの形状を金型で構成しておき、でき上がった製品にタップ加工を施すことも、アウトサート金具を熱圧入することもできます。
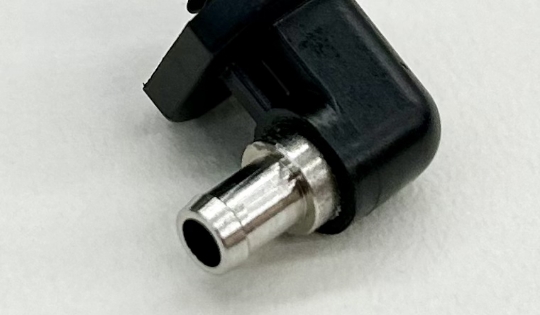
メリット
05
幅広い材料のグレードに対応
切削用の材質(材料のグレード)は限られていますが、射出成形の場合は材料メーカーが出しているグレードが全て生産可能となります。この点は非常に大きなメリットになります。
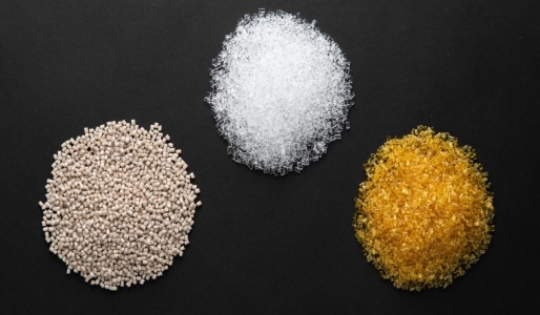
切削部品を射出成形に置換する際の5つの懸念点
切削部品を射出成形に切り替えをする際の懸念点(デメリット)をご紹介します。
懸念点
01
射出成形用の金型費が必要になる
金型は高価なものですが、製品(部品)の生涯生産数により、金型費を生産数で割れば、切削加工品を大きく下回る可能性が高いです。御相談次第で、弊社が金型費を負担し、お客様の御注文数により単価を見積もらせていただくことも可能です。そうすることにより、お客様の資産管理がなくなり、減価償却などの経理処理も不要になります。
懸念点
02
寸法精度
精密機械加工品には及びません。しかしながら、指先に乗るようなサイズであれば、100分台での管理が可能ですし、手のひらに乗るサイズでもコンマ台での管理が可能です。
懸念点
03
形状
射出成形品は溶融したプラスチックが固化する過程で収縮します。収縮率はプラスチックの種類により異なります。例えばPEEKのナチュラルグレードの場合1.3%程度収縮します。その収縮により、偏肉部ではヒケが出たり、長尺ものでは反りが出たりします。
お客様の御使用勝手をお伺いし、影響を及ぼさないように射出成形品向けに設計提案をいたします。
懸念点
04
ゲート(湯口)跡
金型に溶融した材料を注入するため、そのための入り口(ゲート)が必要になります。金型の構造にもよりますが、製品(部品)のどこかにそのあとが残ります。通常はゲートをニッパー等でカットしますが、カットした跡は残ります。
ゲート位置に関しまして、御使用上許容いただける範囲を打ち合わせにてお伺いさせていただきます。
懸念点
05
突き出しピン跡
金型から成形品を取り出す際にピン等で突いて取り出します。そのピンの跡が残りますので、許容いただける範囲を打ち合わせにてお伺いさせていただきます。
1個から量産します
射出成形と言えば、1ロットの生産数が数万個、少なくとも数百個単位で生産するイメージがあると思いますが、
弊社では1個から対応いたします。もちろん1ロットの生産数により単価は異なりますが弊社では量産1個から生産する体制を整えております。お問い合わせをお待ちしております。
ご依頼の流れ
STEP
01
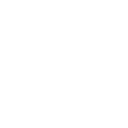
お問い合わせ
まずは、お問い合わせフォームからご連絡ください。
STEP
02
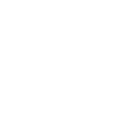
打ち合わせ/見積
お打ち合わせをさせて頂き御見積を提出。3Dプリンタで形状のご確認を頂くことも可能です。
STEP
03
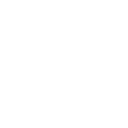
試作
試作テストを実施いたします。
STEP
04
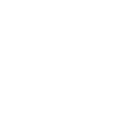
量産
試作テストで問題ないことを確認できましたら量産して参ります。
ダイプラのPEEK加工について
10社以上100製品を超える納入実績があります
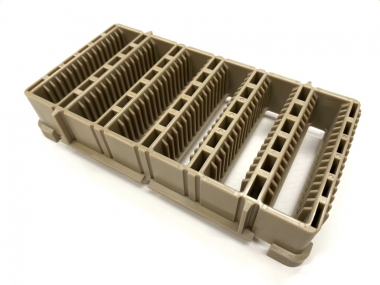
弊社は1988年頃より、当時はあまり用途が見当たらないPEEKの射出成形の技術開発に着手致しました。PEEK加工の詳細は下記からご覧いただけます。