【驚異の高性能樹脂】PEEKとは?特徴・用途・加工のコツまで徹底解説
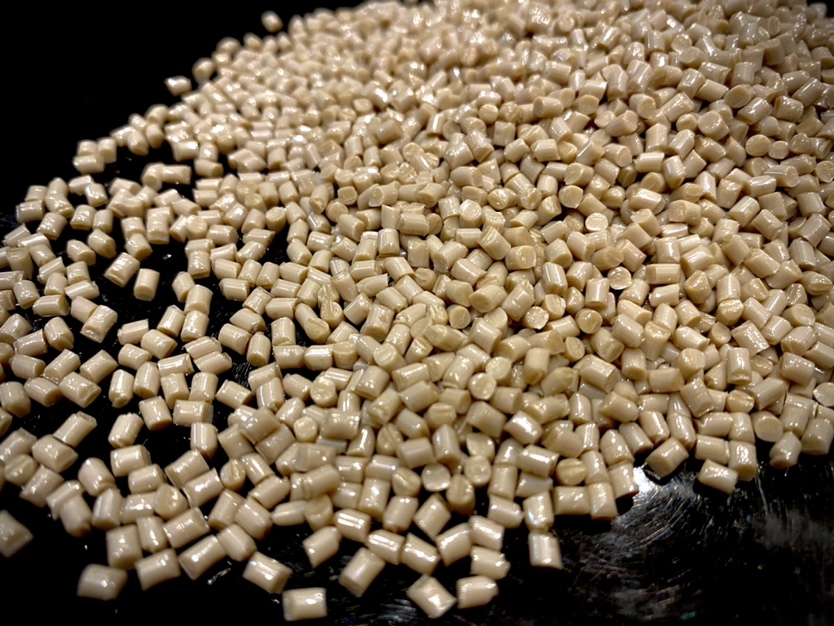
高機能樹脂の中でも、圧倒的な性能を誇る「PEEK(ポリエーテルエーテルケトン)」。その優れた耐熱性・耐薬品性・機械的強度から、医療・航空・半導体・自動車など、最先端分野で注目を集めています。本記事では、PEEKの基本特性から用途、加工の難しさ、そして優れた加工技術を持つ企業の事例まで、わかりやすく解説します。
PEEKの射出成形についてはこちらをご覧ください。
- PEEKとは?スーパーエンプラの頂点に君臨する素材
- 1. 高耐熱性:343℃の融点、260℃の連続使用が可能
- 2. 優れた耐加水分解性と耐蒸気滅菌性
- 3. 機械的強度・剛性に優れる
- 4. 圧倒的な耐薬品性
- 5. 難燃性・低発煙性
- 6. 生体適合性・安全性の認証もクリア
- PEEKの用途|医療から半導体まで多岐にわたる
- 1. 医療分野|体内インプラントから手術器具まで
- 2. 半導体・電子部品分野|クリーンルーム対応素材として重宝
- 3. 自動車分野|軽量化と高機能化を同時に実現
- 4. 航空・宇宙分野|軽くて燃えにくい!それがPEEK
- その他用途
- PEEKのグレード|用途に応じたラインアップ
- 1. 【基本グレード】汎用性が高く、多用途に対応
- 2. 【ガラス/カーボン繊維強化グレード】高強度・耐摩耗を実現
- 3. 【導電グレード(カーボン粒子/CNT配合)】帯電防止・放熱性を強化
- 4. 【医療グレード】生体適合性と規格準拠を重視
- 5. 【摺動グレード(PTFE・グラファイト配合)】摩耗環境に強い
- 【注目ポイント】「ガラス50%成形」など特殊対応も可能
- PEEK加工の難しさと成功のカギ
- 1. 高温・高圧が必須の成形条件
- 2. 成形ロスがコストに直結する高価格素材
- 3. 結晶化制御による物性差への対応が必要
- 4. 射出成形機の選定が成否を分ける
- 5. 長年のノウハウと技能がモノを言う加工領域
- 成功のカギは「設備×設計×職人技」の三位一体
- PEEKの加工事例
- PEEK加工は弊社にお任せください
- 高機能樹脂のプロフェッショナルとして
PEEKとは?スーパーエンプラの頂点に君臨する素材
PEEK(ポリエーテルエーテルケトン)は、スーパーエンジニアリングプラスチック(スーパーエンプラ)に分類される高性能熱可塑性樹脂の一種です。その名の通り、分子構造にエーテル結合とケトン基を繰り返し持ち、これにより高い耐熱性・耐薬品性・機械的強度・電気絶縁性といった特性を同時に実現しています。
特に、PEEKは以下のような点で「スーパーエンプラの中でも最上位」とされる理由があります。
1. 高耐熱性:343℃の融点、260℃の連続使用が可能
一般的なエンプラ(例:PPS、PAIなど)でも耐熱性はありますが、PEEKはその中でもトップクラス。たとえば、連続使用温度は260>℃に達し、自動車のエンジン回りや航空機エンジン周辺といった、極端な高温環境でも物性を維持します。
2. 優れた耐加水分解性と耐蒸気滅菌性
PEEKは高温・高圧の蒸気にも劣化しにくく、オートクレーブ(高圧蒸気滅菌)への繰り返し使用に耐えます。これにより、医療器具や滅菌を繰り返す実験器具など、衛生管理が求められる現場に最適です。
3. 機械的強度・剛性に優れる
引張強度は90MPa以上、カーボンやガラス繊維との複合でさらに強化可能です。従来は金属でしか実現できなかった部品も、PEEKで代替することで軽量化・耐腐食性向上が可能となり、製品全体の効率化や長寿命化に貢献します。
6. 生体適合性・安全性の認証もクリア
日本の食品衛生法、米国FDAなど各種法規にも準拠しており、医療機器や食品加工設備への使用実績も豊富です。さらに、生体適合性にも優れるため、体内埋込型の医療デバイス(人工関節やスパインインプラントなど)への使用も広がっています。
PEEKの用途|医療から半導体まで多岐にわたる
PEEKはその卓越した性能から、さまざまな業界で「金属や他樹脂の代替材料」として選ばれています。ここでは主要な4業界における具体的な用途と、PEEKが選ばれる理由をご紹介します。
1. 医療分野|体内インプラントから手術器具まで
PEEKは生体適合性に優れ、耐滅菌性も高いため、体内・体外を問わず医療用途で幅広く使用されています。
主な使用例:
- 脊椎固定具(スパインインプラント):金属の代替としてMRI対応が可能。
- 人工関節や義歯のベース素材:生体との親和性と耐久性に優れる。
- 注射針ガイド、内視鏡パーツ:高精度で寸法安定性が必要な微小部品。
- 再利用可能な手術器具:オートクレーブに耐えるため長期使用が可能。
PEEKはX線透過性を持ち、CT・MRIの画像に金属アーチファクトを残さないため、術後の診断にも有利です。
2. 半導体・電子部品分野|クリーンルーム対応素材として重宝
半導体業界では、PEEKの低アウトガス性・耐薬品性・耐熱性が高く評価されています。
主な使用例:
- ウェーハ搬送トレイ(チップトレイ)
- リテーナー、フィルター構成材、検査用治具
- フッ酸系薬品に接触するパーツ
クリーンルーム内で使用されるため、微粒子発生が少ないこと、薬品との長時間接触に耐えることが求められます。特に成形精度が要求される用途では、0.1mm以下の寸法公差で成形可能な技術が不可欠です。
3. 自動車分野|軽量化と高機能化を同時に実現
近年、自動車の電動化・高性能化にともない、PEEKの採用が進んでいます。
主な使用例:
- エンジンルーム内の絶縁コネクタ
- 燃料システムのバルブシート、ポンプ部品
- ギア、ベアリング、シャフトブッシュなど摺動部品
高温下(200>℃以上)でも変形しにくく、また潤滑剤が使いにくい箇所でも低摩擦を維持できる点が、自動車業界において重宝されています。
4. 航空・宇宙分野|軽くて燃えにくい!それがPEEK
航空機や宇宙機器において、PEEKは「軽量性・難燃性・耐放射線性」の三拍子が揃った素材として注目されています。
主な使用例:
- 配線用コネクタ
- 断熱材のスペーサー部品
- エンジン周辺の構成パーツ
たとえば宇宙開発では、放射線に強いPEEKが電子機器の保護材や構造材に使われており、実際に宇宙空間へ打ち上げられた部品でも使用実績があります。
その他用途
PEEKは以下のような分野でも導入が進んでいます:
- 食品加工機:食品衛生法適合グレードにより、安全な接触素材として使用可。
- 分析機器・理化学装置:溶剤耐性と高精度成形が求められる。
- 電気絶縁体・ソケット類:高温・高圧下での絶縁性を保持。
このように、PEEKは「過酷な環境でも使える樹脂」として、様々な分野で金属や他プラスチックの代替を実現しています。単に「耐熱性がある」だけでなく、「耐薬品性・耐摩耗性・生体適合性」など多様な性能を持ち合わせている点が、PEEKが唯一無二の素材といわれる所以です。
PEEKのグレード|用途に応じたラインアップ
PEEKは、用途や求められる性能に応じてさまざまなグレードが存在します。ベースとなる特性を活かしつつ、機械的強度・摺動性・導電性・生体適合性など、目的に特化した機能性を追加したグレードが各メーカーから展開されています。
ここでは代表的な5つのグレードについて、より詳細に解説します。
1. 【基本グレード】汎用性が高く、多用途に対応
PEEK樹脂そのものの性能を最大限に活かしたスタンダードなグレードです。寸法安定性、耐熱性、耐薬品性、機械的強度といった、PEEK本来の特性をバランスよく備えており、試作から量産まで幅広い用途に対応可能です。
用途例:
- 半導体関連部品(治具、トレイ)
- 医療用のハウジング部品
- 分析機器の筐体・構成パーツ
2. 【ガラス/カーボン繊維強化グレード】高強度・耐摩耗を実現
PEEKにガラス繊維やカーボン繊維を加えることで、剛性・引張強度・寸法安定性をさらに向上させたグレードです。特にカーボン繊維強化グレードは摩耗性にも優れ、摺動部品や構造材に適しています。
強化の違い:
- ガラス繊維強化:剛性・クリープ耐性が高く、構造材向き
- カーボン繊維強化:剛性に加え、耐摩耗性・放熱性も向上
用途例:
- 自動車や航空機の機械的ストレスがかかる部品
- 高精度・高負荷のベアリングケース、ブッシュ
3. 【導電グレード(カーボン粒子/CNT配合)】帯電防止・放熱性を強化
絶縁性が高いPEEKに、導電性のあるカーボンブラックやカーボンナノチューブ(CNT)を配合したグレードです。静電気の発生を防ぐ必要がある電子部品や、放熱が求められる高集積回路の筐体部品などに最適です。
特徴:
- 表面抵抗値を制御可能(10⁶~10⁹Ω/□など)
- CNT配合により、体積抵抗と強度を両立可能
用途例:
- 半導体製造装置内の静電対策部品
- 放熱が必要な電子基板カバー
4. 【医療グレード】生体適合性と規格準拠を重視
ISO10993やUSPクラスVIなど、生体適合性や医療機器認証に対応したグレードです。インプラント材としても使用されるほど安全性が高く、人体との長期接触が前提となる製品に使用されます。
特徴:
- MRI非干渉素材として使用可能
- 滅菌耐性あり(オートクレーブ、エチレンオキサイド滅菌など)
用途例:
- スパインケージ、関節インプラント
- 外科用ナビゲーション器具、穿刺器具
5. 【摺動グレード(PTFE・グラファイト配合)】摩耗環境に強い
PEEKに潤滑材として知られるPTFE(四フッ化エチレン)、グラファイト、炭素繊維などを加えることで、自己潤滑性・耐摩耗性を向上させたグレードです。潤滑油を使用しにくい環境でも長寿命を実現します。
特徴:
- 摩擦係数が大幅に低下(0.1以下)
- 摩耗による微粒子の発生も少ない
用途例:
- ギア、スライドブッシュ、ピストンリング
- 高速摺動が必要な機械部品、食品製造装置の可動部
【注目ポイント】「ガラス50%成形」など特殊対応も可能
一般的にガラス繊維の高充填成形は難しいとされていますが、加工技術次第でガラス50%充填PEEKなど特殊グレードへの対応も可能です。これは成形設備と職人技術の両面が揃ってこそ実現できる領域です。
このようにPEEKは、「特定用途に最適化されたグレード設計」が可能な樹脂です。使用環境や設計要求に応じて適切なグレードを選定することが、製品の長期的な信頼性とコストパフォーマンスを高める鍵となります。
PEEK加工の難しさと成功のカギ
PEEKは「高性能=加工が難しい」素材の代表格です。優れた耐熱性や機械的強度の裏には、極めて高い融点・粘度・結晶性という特性があり、これらが一般的な樹脂成形と大きく異なる加工上のハードルを生み出しています。
ここでは、PEEK加工における主な難点と、それを乗り越えるための成功要因について詳しく解説します。
1. 高温・高圧が必須の成形条件
PEEKは**融点が343>℃、成形時のシリンダー温度は400~450>℃、金型温度は160~200℃**という非常に高温領域での成形が必要です。これは、汎用樹脂の約2倍以上の温度帯であり、一般的な成形機では対応が困難です。
また、粘度が非常に高く流動性が低いため、高い射出圧力と保圧制御が要求されます。これを実現するには、耐熱・高圧対応の**専用成形機(高温スクリュー、加熱筒、冷却機構)**と、正確な温度制御機能が必須です。
2. 成形ロスがコストに直結する高価格素材
PEEKは1kgあたり1万円以上という非常に高価な素材です。金型設計や成形条件が最適化されていない状態で試作・量産を行うと、1ショットのロスが数千円~数万円規模になることもあります。
そのため、ロス最小化=コスト競争力の確保という観点からも、素材特性を理解したうえでの金型設計・ゲート設計・離型処理・温度管理が極めて重要となります。
3. 結晶化制御による物性差への対応が必要
PEEKは半結晶性樹脂であるため、金型内での冷却速度や保温状態によって結晶化度が変化し、寸法や機械的性質に大きな影響を与えます。
たとえば、金型温度が低すぎると結晶化が不十分となり、強度が落ちたり、寸法安定性が悪くなる場合があります。一方で過剰な冷却時間は生産性を著しく低下させます。
→ 最適な結晶化を実現する金型温度と冷却管理が、品質と効率の両立の鍵となります。
4. 射出成形機の選定が成否を分ける
PEEKのような高粘度・高温樹脂には、強力なトルクと加熱性能を持つ専用機械が必要です。たとえば、株式会社ダイプラではドイツ製「アーブルグ」の油圧式射出成形機を採用しています。
この成形機は、電動式並みの精密制御を備えつつ、油圧式ならではのパワーで高粘度樹脂を安定成形できる点が強みです。さらに、450℃対応の加熱筒を標準装備しており、PEEKの本格量産にも対応しています。
5. 長年のノウハウと技能がモノを言う加工領域
成形条件が厳しく、ロスコストも高いPEEKにおいては、トライ&エラーの蓄積と経験値が非常に重要です。
たとえばダイプラでは、36年以上にわたるスーパーエンプラの成形経験により、以下のような高度な対応が可能です:
- 薄肉成形(0.5mm厚 × 60mm角など)
- 大型成形品(1ショット300g超)
- 0.1mm以下のピッチ公差制御
- インサート成形・PEEK同士の溶着技術(封止成形)
このような技術の積み重ねにより、製品精度・歩留まり・コスト最適化を同時に実現しています。
成功のカギは「設備×設計×職人技」の三位一体
PEEKの加工は「機械さえあればできる」ものではありません。最終的な成功を左右するのは、
- 高温・高圧対応の設備
- 精緻な設計と金型管理
- 素材特性を熟知した技術者の経験と対応力
この三要素の融合です。
高性能素材を活かしきるには、それに見合った加工技術と体制が不可欠。だからこそ、PEEK製品の製造を委託する際は「単なる成形業者」ではなく、「PEEKの専門技術を持つ加工パートナー」を選ぶことが重要なのです。
PEEK加工は弊社にお任せください
PEEKは「高性能であるがゆえに難加工」な素材であり、量産で高品質を安定的に実現するには、設備・技術・経験すべてが求められます。株式会社ダイプラでは、35年以上にわたりPEEKをはじめとするスーパーエンジニアリングプラスチックの成形加工に取り組み、数百種類におよぶ製品開発を行ってきました。
「ロスを抑えた高効率な成形」「薄肉・大型といった難易度の高い形状への対応」「PEEK同士の接合やインサート成形」など、他社では難しい加工も高精度・高再現性で実現可能です。
PEEKの射出成形についてはこちらをご覧ください。
すべての成形機がPEEK対応:アーブルグ製射出成形機11台保有
弊社が保有する11台の成形機は、すべてドイツ・アーブルグ社製。
油圧式ながら電動機並みの精密な射出制御を実現し、高粘度で高い射出圧力が必要なPEEKにも安定的に対応します。
- 加熱筒最高温度:450℃
- PEEK向け金型温調機:200℃以上に対応
- 1ショット最大重量:300g以上対応可
試作~量産までワンストップで対応
- 図面のない状態からの相談OK
- PEEKグレード選定・流動解析にも対応
- 量産向け金型製作から品質管理まで対応
(御要望があれば試作型製作を経て良好な量産まで対応)
加工だけでなく、「開発段階からの設計・技術支援」や「加工性を考慮した形状提案」など、開発パートナーとしての役割も果たします。
高機能樹脂のプロフェッショナルとして
PEEKは高価で高機能な素材だからこそ、無駄なく、適正に加工できるパートナーの選定が最重要です。
「PEEK製品を検討しているが、どう進めればよいかわからない」
「他社に断られたが、どうしてもPEEKで成形したい」
そんなご相談も、ぜひダイプラにお任せください。
企画段階(ポンチ絵レベル)からのサポートも承ります。
まずはお気軽にご相談ください。